We have an order on our system that was created 23/02/24. It had 1 line item, with a qty of 1 required. Today (07/03/24) I added another line for the same item, with a qty of 1.
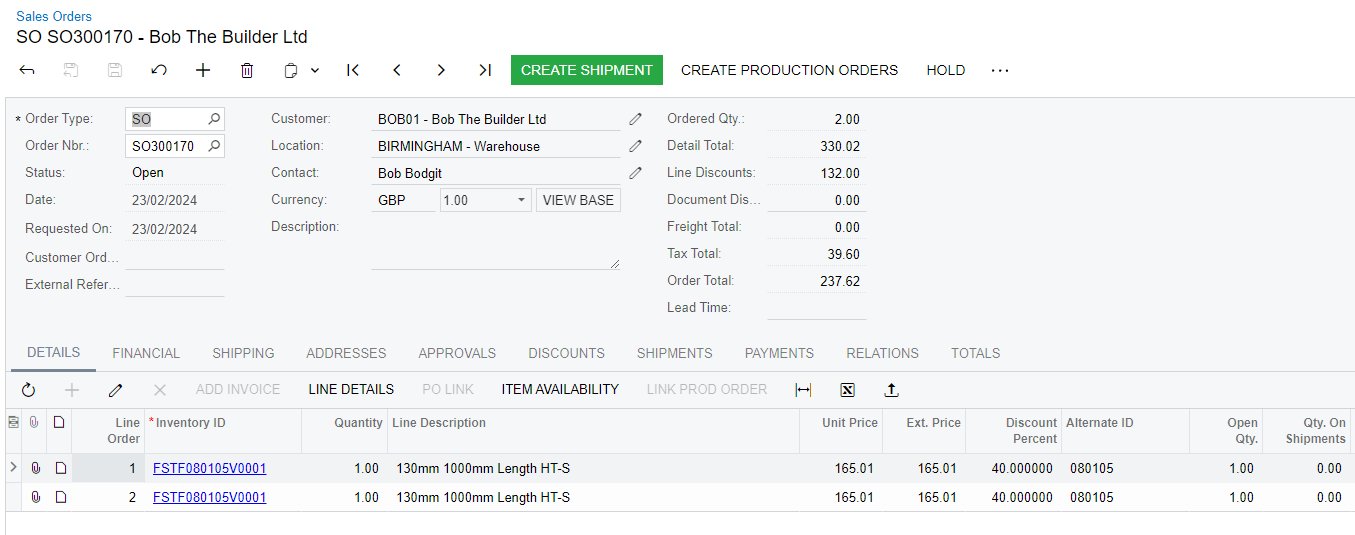
When I then Create Shipment, the original item populates the Shipped Qty with 0, but the new item populates the Shipped Qty with 1.
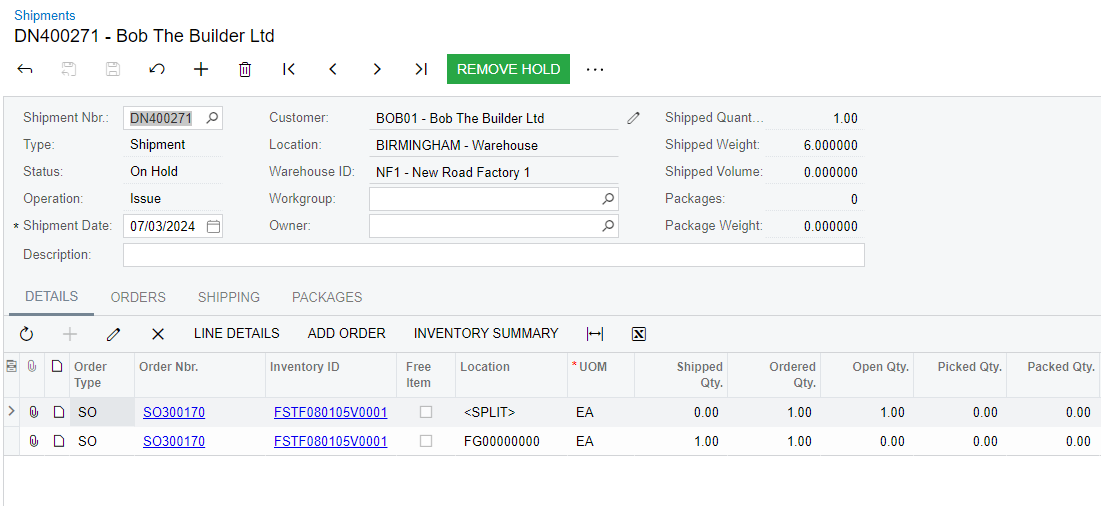
The behaviour we want is as per the original item - i.e. the Shipped Qty should remain 0 until we actually pick/ship the item.
We’ve noticed that the Location shows <SPLIT> for the original item and FG000000 for the new item - not sure if this is related?
Note: we have only edited the original order to demonstrate the different behavior, our new orders behave as the added line does, which is not what we want.
We have tried editing various settings, but cannot get new orders to behave as we’d like.
It seems as if when the original Sales Order was created there was item/setup data recorded that makes the Shipment behave in a certain way for the existing item.
But when you add a new item, the item/setup data isn’t the same and it makes the Shipment operate differently.
Any thoughts?
TIA