there is available inventory but i am still getting this message.
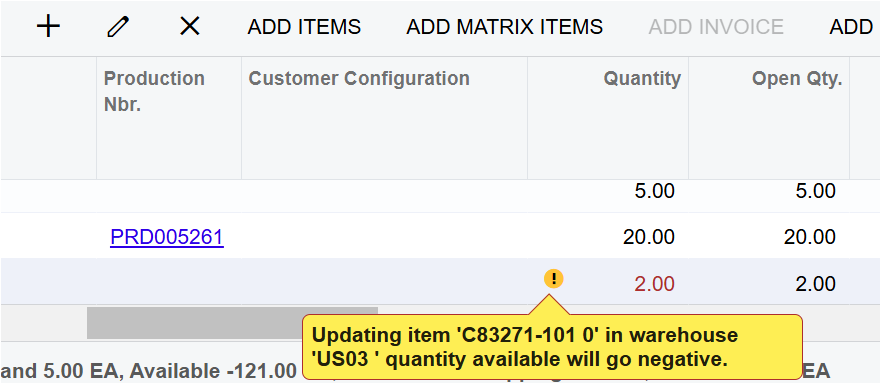
There is enough availability on hand. i am only allocating 2 pcs and the system shows 5 available between my two shipping locations.
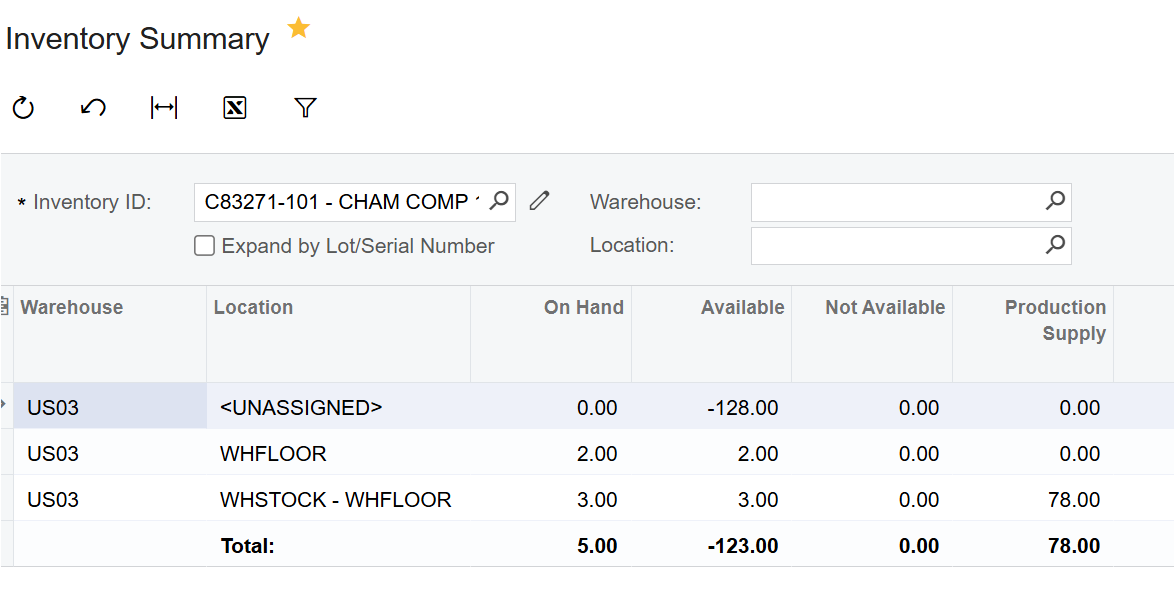
i’ve checked Inventory Allocation Details but i'm not sure how to read it. but i did check all the sales orders with this part number and i don't have any allocated as show in Inventory summary above.
Any help in pointing me in the right direction would be great.