Client is creating the production order the day before the actual production run estimating how many cases will be produced so they can print off the FG bar codes. They are also setting up the release of materials so the raw pallets and caps can be scanned in real time. The issue is that they cannot change the number of cases produced after the release of materials is made (without deleting the release of materials, which defeats the purpose of scanning real time) they wont know the exact number of cases produced until after the shift is done producing. Any thoughts on how to change the production work order flow that allows one order per shift and the modification of the produced qty in that work order before completing production order in system.
Solved
Produced Qty not known till after production ruun
Best answer by aiwan
Hi
Stupid question but just to make things clear, do they use the move screen?
I’m assuming so, if the below is changed to “Allow”, this should let the client run through with as much as they need and overproduce the production order based on the initial qty.
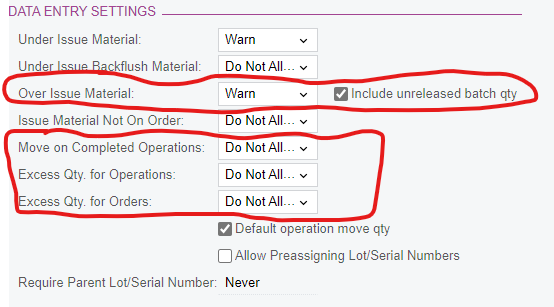
I apologise in advance if i have hugely misunderstood your requirement!
Reply
Enter your E-mail address. We'll send you an e-mail with instructions to reset your password.