We have a manufacturing prospect that produces thermoplastic products using the roto-molding process. This allows one or multiple products to be indexed and manufactured on the same machine. I need help figuring out a way to set up work centers to optimize machine efficiency and production schedule.
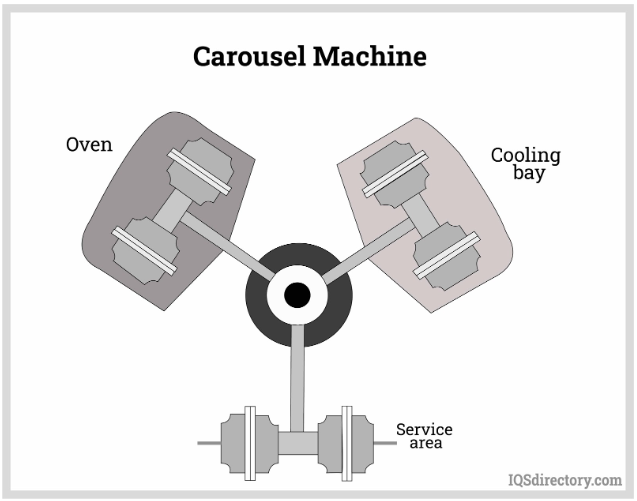
In a nutshell, the molding machine is on a carousel with 3 indexing arms - one for unloading FG/loading materials, one for heating/molding, and one for cooling. For large-size products, each arm can only handle one unit of one SKU. For medium-size products, each arm can handle 2 units (i.e., a 2 x 1 unit configuration) of the same or 2 different SKUs. For small-size products, each arm can handle up to 10 units (i.e., 2 x 5 units) of the same or 2 different SKUs. Using a dumbbell analogy, I can load 4 x 5lb plates on one side and 2 x 10lb plates on the other.
In short, we can have 1 but potentially up to 6 production orders running on the same machine. For a given BOM, each of the 3 operations (assuming comparable setup time, run time, machine time, queue time, and finish time) can have:
- WC-L for 1 run unit
- WC-M for 2 run units
- WC-S for 10 run units
The point I am struggling with is how to schedule production with a fixed block that has varying production capacity, depending on the chosen work center. In another word, can scheduling be based on block size and product size?