Hi All,
I reviewed some articles and most of them couldn’t answer a very simple Use Case.
In Manufacturing it is very common that more than just screw or other Components Parts are used as they break in the process or other things.
This is technically Scrap that needs (for typical processes) to be logged as Scrap rather than Material Cost against the Production Order.
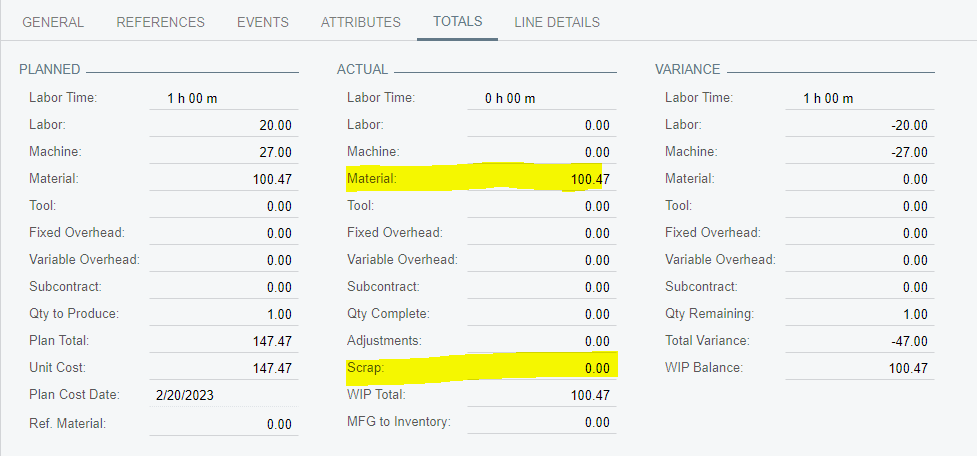
I can’t seem to find a way to accommodate for that kind of Scrap. Scrapping the FG is just completely overstating and doesn’t let the User adjust.
Utilizing a Scrap Factor just adds to Material Cost rather than considering it as actual Scrap Cost.
I would be very surprised if we cannot accommodate for this at all?
This is just so common. Scrap is not the actual Material Cost but separate from Raw Material Cost and needs to be logged - not only for the FG with Scrap write-off.