We have an item that is allocated. It is the last qty that is in stock:

It is allocated to this shipment from this location:

But, when we go to pick the item, we get this error. Our lot class issue method is user-enterable, so we scan the lot number when we pick the item. This is happening repeatedly. Since we are in Pick Pack Ship, we are stuck with leaving the item on back order if we want to get the order out same day, even though all our ducks seem to be in a row. Sorry about the size of the image.
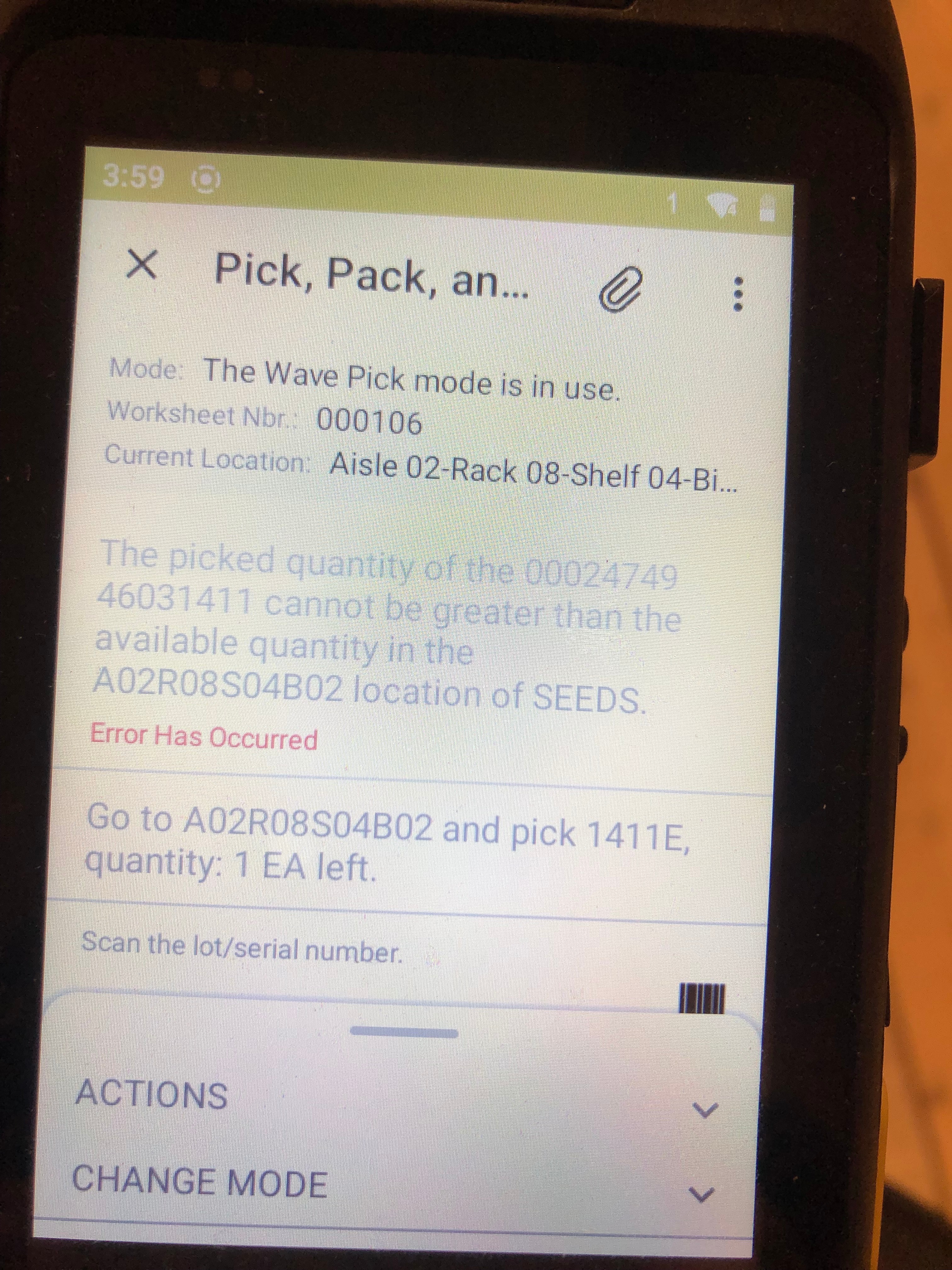