Hi All,
We have item “orange” store in warehouse A - 10 EA; warehouse B - 20 EA; warehouse C - 0 EA. We got a lot of orders from customer need to be delivered from warehouse C. So how can we count how many oranges do we need to transfer to warehouse C to cover available qty for all the customer orders.
Current apply solution:
Option 1: Using Replenishment → set up min stock order for Warehouse based on the average sales.
Disadvantage: when we run Replenishment that will apply for individual Warehouse (WH).
If min order is 30 qty for each WH, run Replenishment will require order WH A - 20 EA, WH B - 10 EA, WH C - 30 EA and 60 EA in total.
However, we can transfer goods from WH A & B to C instead of creating a new order
Option 2: Using require Allocated on Sales Order.
We record new SO as draft SO if that item dont available on that warehouse and the system will reserve that order with negative qty. We can run report Inventory Balance or Storage Summary to see how many negative qty has been recorded on that warehouse and then we know how many goods we need to transfer to that warehouse.
Disadvantage: the negative qty only recorded if there are no qty of that item in warehouse. If the order qty > available qty in warehouse, user need to go to Line Details and uncheck box Allocated (if this box check, SO cant be saved).
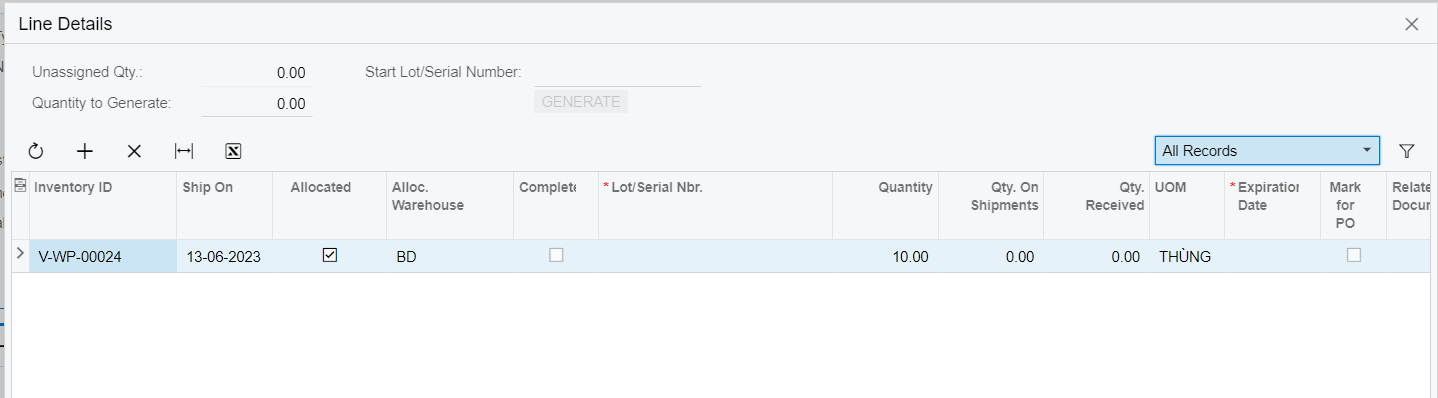
After that, when goods are available in warehouse, user will go to Line Details and check that box again before Creating Shipment.
We have seen above solutions is quite a work around for this base business case.
Therefore, I would appreciate to have your advice on how your company manage the available storage and stock order or if you have any idea on the above case.
Thanks in advance,
Yên Chi