Hi Sir
We would like to know what mean of production variance.
As we do a disassembly transaction and notice that system auto generate “ production variance” May i know what is this for? Please refer to the below.
If based on below journal , does it mean the production variance 21.44 is reduce the inventory value as the double entry is credit account code14720 inventory.
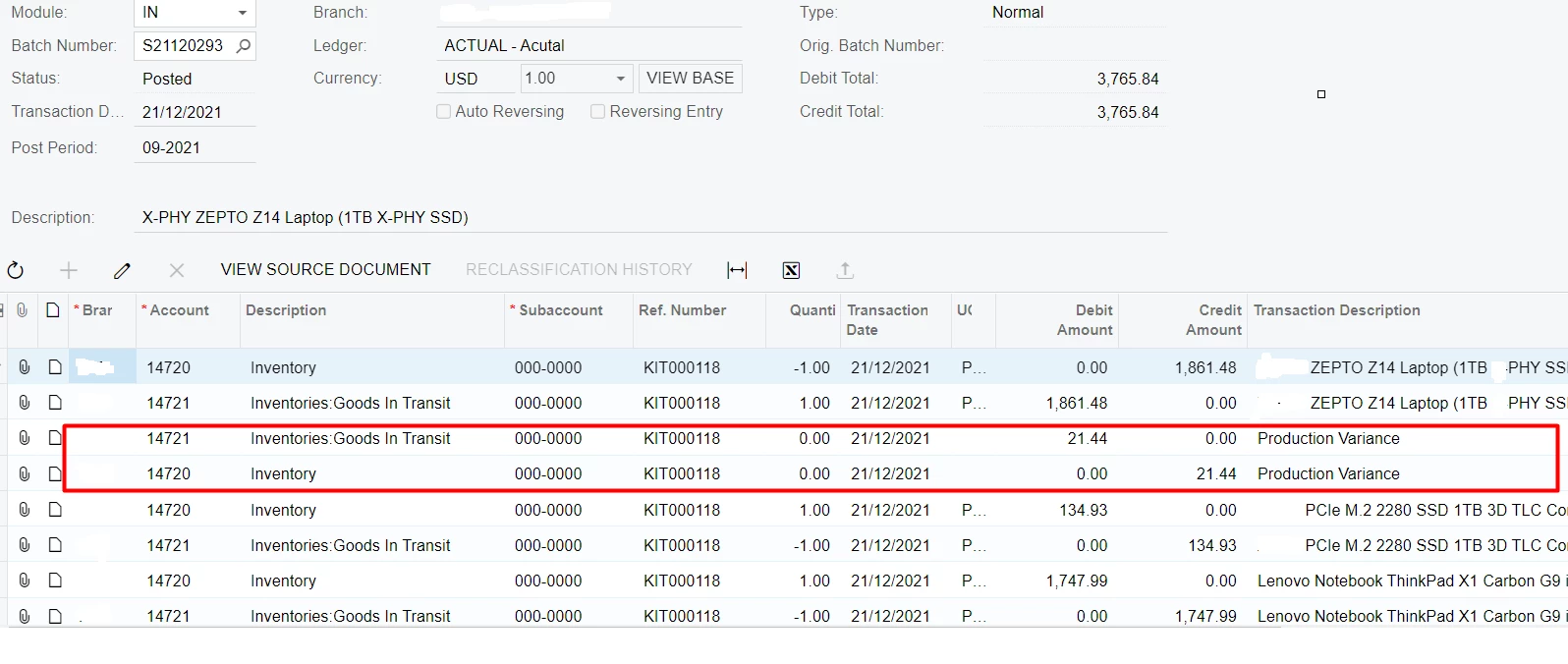
Best answer by PaulMainard55
View original