I have a customer who has been anxiously waiting for the ability to complete a 2-step transfer on the mobile app. I see now that you can actually select Transfer Receipt as on option under Purchase Receipts:
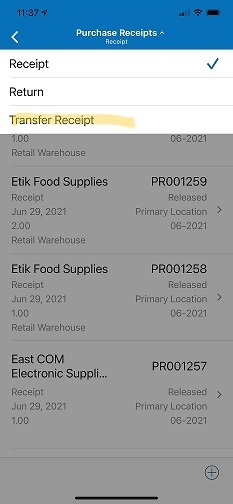
However, all I seem to be able to do is create the record. I can’t find anywhere to enter the Transfer Order to receive. Help?
Thanks!
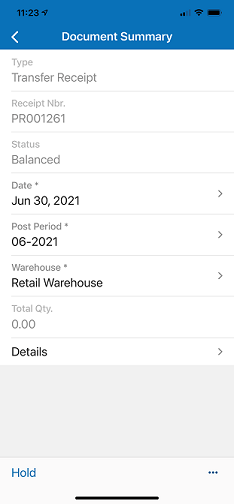
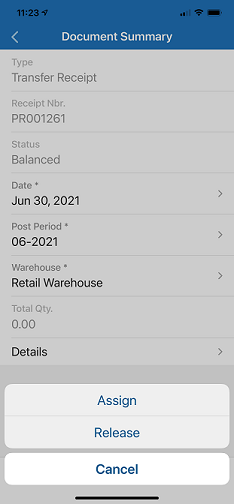