Scenario: A sales order is entered for qty 100 of a manufactured item. A production order is created for all 100 pieces to drive the material requirements.
Only 5 pieces are going to be produced and shipped this week, but when the RELEASE MATERIALS action is selected, Acumatica always puts the total material for the whole production order (unless there are shortages) and the user has to adjust every single line so that material is only released to cover the 5 units being produced (there could be hundreds of line items):
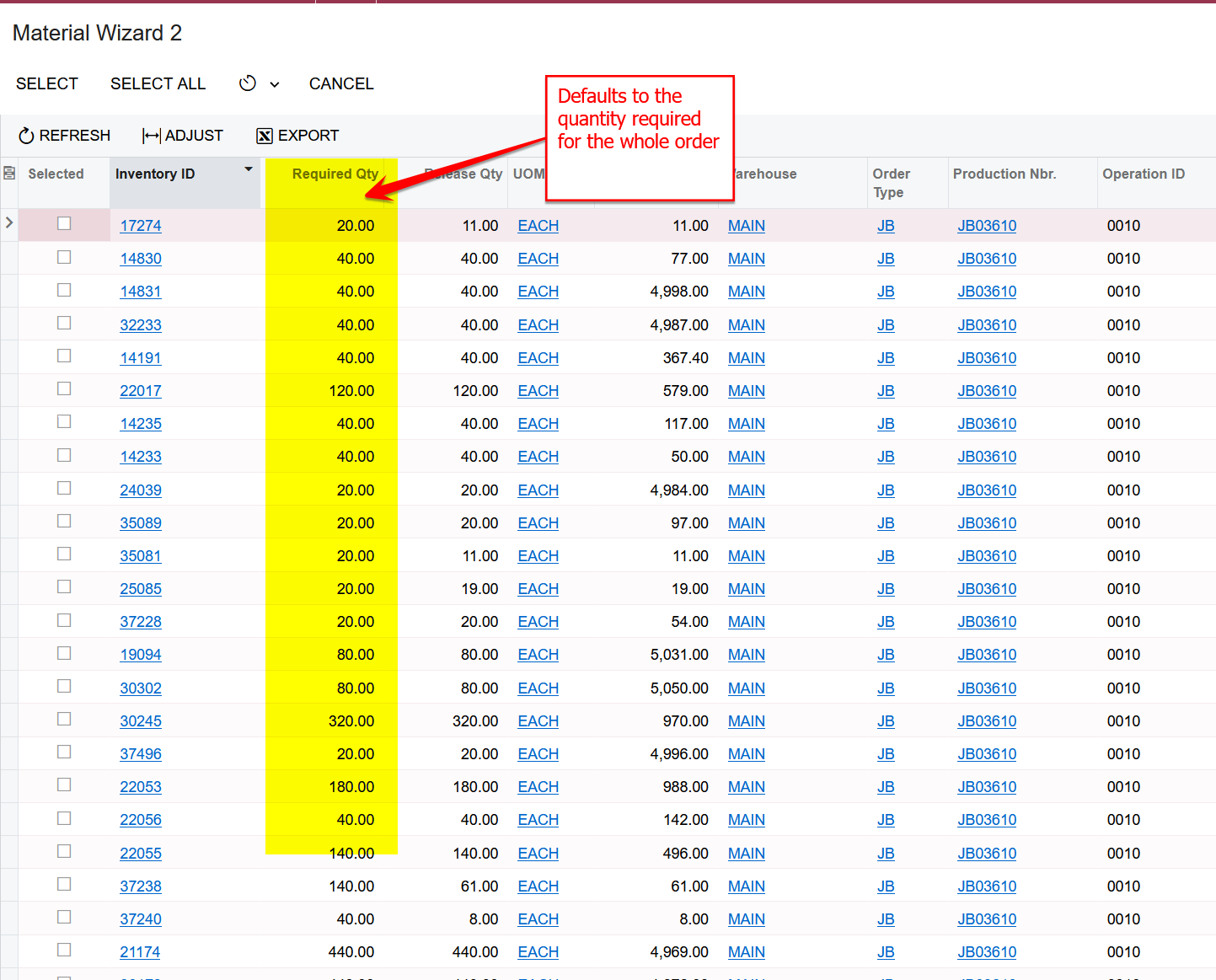
Is there a way to select the quantity to be produced off of the production order, and have Acumatica calculate the required component quantity automatically so that each line doesn’t have to be manually adjusted?
The work around I have them using right now is to export this list from the Material Wizard to excel, use excel to calculate the required quantities for the partial production quantity and then upload the spreadsheet on the Materials screen as a new transaction.
Best answer by Debbie Baldwin
View original